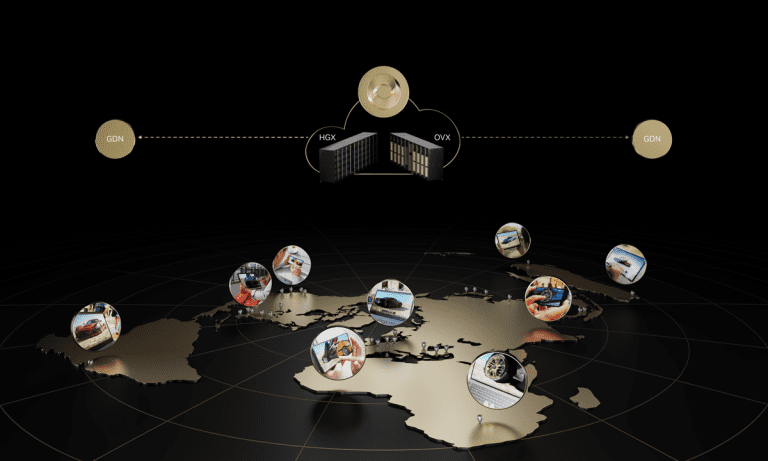
Alors que le scepticisme à l’égard des métavers qui vont « tout changer » s’accroît au fur et à mesure que Meta’s se bat pour produire une réalité virtuelle immersive viable, un nouveau « next big thing » attend dans les coulisses : Le métavers industriel.
Nous examinerons comment les entreprises adoptent les « jumeaux numériques » de leurs usines et installations et les différents cas d’utilisation de la RV d’entreprise et des secondes vies d’entreprise.
Alors, qu’est-ce qu’un métavers industriel et comment sera-t-il utilisé ?
Il existe plusieurs types de métavers industriels, à commencer par les espaces de collaboration où des concepteurs du pays ou du monde entier peuvent collaborer sur un même projet dans un seul espace virtuel, ou encore où les spécialistes du marketing peuvent dévoiler, présenter ou même vendre des produits virtuels – en testant une voiture, par exemple.
Mais une autre valeur réelle du métavers industriel, et peut-être la plus importante, est le jumeau numérique, une recréation d’une usine ou d’une autre installation où les conceptions peuvent être testées et où les problèmes de production peuvent être observés – et ajustés ou corrigés – en temps réel.
La technologie métavers de Nvidia Omniverse Enterprise est utilisée pour construire un jumeau numérique de l’opérateur ferroviaire allemand Deutsche Bahn, qui lui permettra de surveiller en temps réel les opérations de l’ensemble de son réseau de 5 700 gares et de 30 000 km de voies ferrées.
Le métavers vivant
Contrairement à l’Horizon Worlds du PDG de Meta, Mark Zuckerberg, qui a fait l’objet d’une grande controverse, des entreprises telles que Siemens, Boeing, Mercedes et BMW ont déjà mis en place des métavers industriels, selon Digital Engineering.
La Siemens Digital Native Factory de Nanjing, en Chine, a été construite dans le métavers comme un jumeau numérique avant qu’un seul coup de pelle ne soit donné, a indiqué l’entreprise dans un communiqué.
Cela a permis « d’optimiser la construction, de détecter et d’atténuer les problèmes potentiels à un stade précoce », a-t-elle ajouté. « Les erreurs de planification, petites et grandes, qui par le passé auraient coûté beaucoup d’argent et de temps, ont été complètement évitées. Et nous continuons à utiliser le pouvoir de la simulation pendant les opérations. »
La capacité de fabrication a augmenté de 200 % et la productivité de 20 %, selon l’entreprise. Le jumeau numérique photoréaliste lui permet de créer la disposition optimale pour les robots de construction, de tester l’impact des changements de température et même de simuler l’impact des pièces défectueuses.
« Les produits sont extrêmement complexes », a déclaré Tony Hemmelgarn, président et directeur général de Siemens Digital Industry Software, lors d’un débat dirigé par VentureBeat à la conférence virtuelle GTC du constructeur de métavers industriels Nvidia en septembre. » Une automobile a des centaines de milliers d’exigences qui entrent en jeu, ou un avion ou autre. Comment modifier une exigence sans savoir comment elle affecte tout le reste de manière virtuelle ? Si vous ne pouvez pas représenter le logiciel, l’électronique, la conception mécanique ou, mieux encore, la fabrication, l’automatisation et tous les éléments qui entrent dans la fabrication de ce produit, vous ne pouvez vraiment pas le simuler. »
De meilleurs résultats
En décembre, Boeing a révélé qu’il prévoyait de construire son prochain grand avion, le 777X, en utilisant la technologie des jumeaux numériques pour créer des représentations virtuelles en 3D de l’avion et de ses moteurs, ce qui permettra aux ingénieurs de simuler et de tester les conceptions et les modifications en temps réel, selon Reuters. Chaque conception sera soutenue par un « fil numérique » qui s’enfonce dans la chaîne d’approvisionnement avec les exigences de chaque compagnie aérienne, les détails sur les millions de pièces, chaque modification de conception et les milliers de pages de documents de certification requis, ajoute l’agence.
Il s’agit de « changer la façon dont nous travaillons dans toute l’entreprise », a déclaré Greg Hyslop, ingénieur en chef de Boeing, à Reuters, ajoutant que 70 % des problèmes de qualité remontent à des problèmes de conception. « Vous obtiendrez de la rapidité, vous obtiendrez une meilleure qualité, une meilleure communication et une meilleure réactivité lorsque des problèmes surviennent. »
Et avec un peu de chance, éviter des catastrophes comme la faille qui a fait s’écraser plusieurs 737 MAX en 2018 et 2019, arrêtant la production pendant près de deux ans alors que de plus en plus de problèmes potentiels étaient découverts.