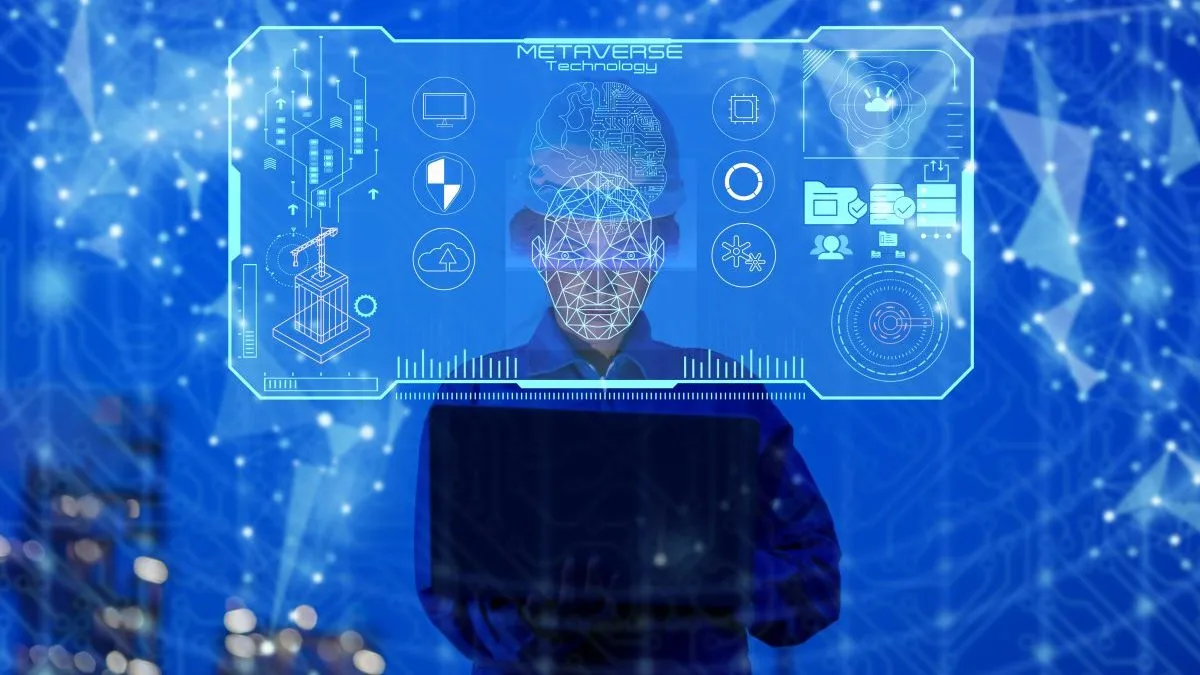
L’industrie manufacturière pourrait devenir la première industrie à adopter les métavers, principalement parce que les métavers ont de grandes chances de résoudre les problèmes rencontrés par les fabricants et qu’il y a eu beaucoup d’investissements dans l’infrastructure IoT industrielle, y compris l’IA et les réseaux privés 5G.
On ne sait pas encore à quoi ressemblerait un métavers, mais il est certain que les réseaux à haut débit, l’apprentissage automatique de l’IA, le cloud/edge computing, le traitement des big data, la technologie AR/VR/MR et la blockchain relient les sensations dans la réalité à des scénarios virtuels, ce qui nourrit le développement des métavers dans le domaine industriel.
L’industrie manufacturière est très demandeuse de métavers ; par exemple, pour faire face à la pénurie de main-d’œuvre, les techniciens supérieurs peuvent transmettre leur savoir-faire aux ordinateurs par des approches numériques.
L’industrie manufacturière peut bénéficier des métavers dans la simulation de l’optimisation des lignes de production et la collaboration à distance pour la réparation et la formation des nouveaux employés, en adoptant la technologie des jumeaux numériques basée sur les métavers.
En utilisant l’IA pour simuler des objets réels, un jumeau numérique permet d’imiter un équipement réel en tant qu’équipement virtuel ayant les mêmes spécifications et peut donc être utilisé pour simuler l’optimisation de l’équipement avant de mettre en place de nouvelles lignes de production ainsi que pour trouver des défauts dans les produits.
Pour la construction automobile, un jumeau numérique peut être utilisé pour simuler la conduite autonome dans des scénarios virtuels pour ajuster les fonctions de détection. BMW a passé six mois à utiliser la technologie du jumeau numérique pour mettre en place une usine automobile virtuelle. Sur la base des recommandations issues de la simulation dans l’usine virtuelle, l’entreprise a révisé 30 % de la conception initiale de l’usine pour innover dans le processus d’assemblage et même raccourcir le délai entre la conception du produit et sa production.
Le jumeau numérique combiné aux dispositifs AR/VR permet la réparation collaborative à distance des équipements défaillants. Seuls les techniciens de réparation doivent rester sur le lieu de la panne, tandis que les ingénieurs peuvent trouver les causes de la panne par le biais de la surveillance à distance et introduire des commandes et des procédures de réparation dans les dispositifs ARVR pour permettre aux techniciens d’entreprendre la réparation sur place. Associée à des robots collaboratifs et à la technologie de vision artificielle, la réparation collaborative à distance peut être accélérée ou un avertissement précoce de défaillance de l’équipement peut être envoyé.
La formation des nouveaux employés basée sur les métavers peut éviter de les exposer à des conditions de travail dangereuses telles que des températures élevées, une pression élevée ou un bruit important, grâce à une formation par immersion dans un environnement de fabrication virtuel. En outre, la formation par immersion leur permet d’être instruits sur le fonctionnement correct des parties cruciales des lignes de production afin d’éviter les erreurs irrémédiables. En outre, cette méthode de formation permet d’économiser les coûts de transport vers les usines pour la pratique sur le terrain.
Si les avantages susmentionnés sont à court ou moyen terme, les avantages à long terme pourraient être des solutions innovantes pour les processus de fabrication ou la gestion des matériaux grâce à l’intégration des données des différentes usines d’un fabricant dans une usine virtuelle, voire la connexion des données intégrées avec les données des fabricants de la chaîne d’approvisionnement.